Minimize energy costs with the Energy Optimizer
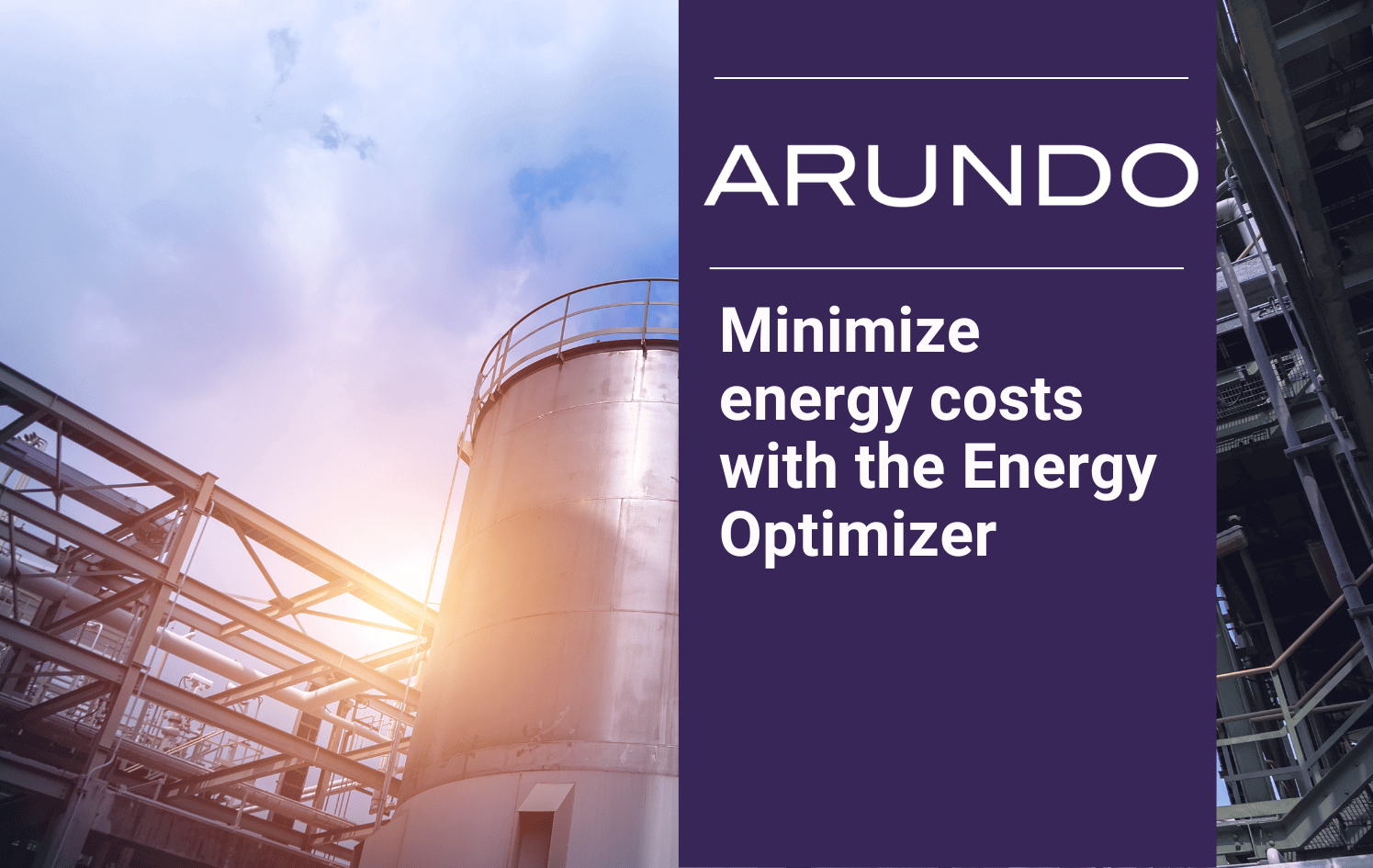
As recent geopolitical events and the transition away from fossil and nuclear fuels have led to higher and increasingly volatile energy prices in Europe, reducing energy costs is now a top priority for all affected industrial companies.
This is not only limited to running machinery at optimal efficiency, but also adjusting production to take advantage of spot price variations. This naturally gives direct savings for electricity purchased on the spot market, but also creates the opportunity to sell back during peak hours for fixed-price contracts. In addition, reducing consumption at peak demand has environmental and societal benefits: CO2 emissions are reduced as the fossil-fuel component of the energy mix is the highest at peak demand, and reducing peak demand is an important contributor to grid stability.
One industrial process which can greatly take advantage of the Energy Optimizer is electrolysis.
In this whitepaper, we show results from optimizing the chlor-alkali process. The realizable electricity cost savings potential is on the order of 3-5%, with an absolute potential of 15%, limited by spare production capacity, electricity prices, forecast accuracy, and often and by how much the electrolysers can be adjusted during operation.
Contents:
- Introduction
- Key takeaways - exec summary
- Why is this important now?
- Energy Optimizer in a nutshell
- Example process: Chlorine electrolysis
- Background: The chlor-alkali process
- INEOS Inovyn case study
- Conclusion